Understanding Thermal Movement in Metal Roof Systems
Sheet-metal roofing systems can truly stand the test of time. We can find them dating back to the World War II era. Even today, roofing contractors are often struck by the level of craftsmanship and precision that went into the sheet metal systems found on historic buildings and structures. These roofing systems have a few engineering characteristics that enable them to last. The most notable one is the ability to accommodate thermal movement. (Expansion and Contraction)
Metal roofs are typically the standard for large commercial and industrial buildings. The characteristics of sheet-metal panels are advantageous for many industries, especially those with critical manufacturing environments prone to intense heat. However, if thermal movement is restricted somehow – that’s when we begin to see system failures in as little as five years.
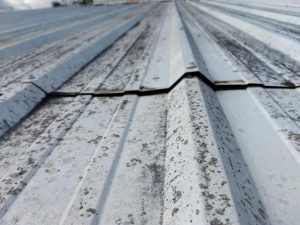
Basic Principles of Thermal Movement
The principles behind thermal movement are often misunderstood. That’s why it’s essential to understand the properties of thermal activity if you want your roof system to last as long as possible.
The manifestation of thermal movement isn’t visible to the naked eye – as it happens in real-time. Instead, what we eventually see in failures from thermal movement has been happening for years. It has been many years of thermal cycles(seasons) in most cases.
Because of the time allowed to pass before any issues are visibly seen, it can be challenging to pinpoint precisely how the failure began. Installers will be long gone by that time. And in some cases – so will the original maintenance staff and/or building owners. This situation potentially leaves failures caused by thermal movement misdiagnosed as something else. Blame usually gets shifted over to improper installation practices or poor craftsmanship.
A few factors contribute to how much thermal movement will occur on a sheet-metal roofing system.
- Metal type
- Length of the panel
- The temperature of base metal
- Solar radiation directly affects ambient air temperature (which also plays a role)
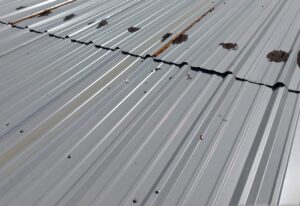

The Coefficient of Expansion is Constant for All Metal Thicknesses
So there would be no deviation expansion rate from a 24-gauge and a 26-gauge panel.
*Note – Stainless steel and copper are very close in expansion/contraction rates. How will that affect the fastener and the roof purlin?
A concealed fastening system is mostly used with copper, so movement handled with traditional (through – screws) will fail due to over-expansion and contraction of stainless steel.
_______________________________________________________________________________________
Metal Type | Coefficient of Expansion (per 1 degree F) | Change in Temperature | Expansion and contraction in a 10-foot section | Expansion and contraction in a 40-foot section |
Aluminum | .0000129 | 200 F | 0.3096 inches | 1.2384 inches |
Galvanized Steel | .0000067 | 200 F | 0.1608 inches | 0.6432 inches |
Stainless Steel | .0000096 | 200 F | 0.2304 inches | 0.9216 inches |
Copper | .0000098 | 200 F | 0.2352 inches | 0.9408 inches |
______________________________________________________________________________________________
Important Definitions
Fixed Points
Metal systems are most durable when able to float in at least one direction. Fasteners used as fixed points will direct thermal movement away from the fastener. Examples of fixed points can include fasteners near the ridge of a standing seam panel that penetrates the substrate.
Absorption of Thermal Movement
Thermal movement absorption appears in flat-lock metal systems and standing seam panels. The movement is absorbed into the seams and cleats, where it is then guided upward into the panel and contained. This process is the opposite of accumulated thermal movement. Proper design of Flat-Lock systems includes a maximum panel length of 18X24 inches for copper and stainless steel.
Built-In Gutter Systems
Knowledge of thermal movement properties for stainless-steel and copper should also be considered when selecting metal for built-in gutter systems and liners. Galvanized steel systems are much better suited for gutters and liners for the same reason as in panel selection. Less Thermal Movement.
Note: Steel liners are susceptible to corrosion when not maintained appropriately (painted). However, they’re still much less likely to fail from restricted movement.
When selecting underlayment materials for gutters and panels alike, the same information comes into play. The underlayment is used as protection against moisture that comes in contact with the underside of system panels and gutters. Excess moisture will cause corrosion if not controlled properly.
Maintenance and Repairs
It’s imperative to understand, plan, and accommodate for thermal movement BEFORE installing any metal roofing project. Miscalculating or ignoring the physical properties of necessary materials can lead to unwanted and costly unintended repairs.
The takeaways are simple. Contractors and building owners need to be aware of the physical properties of their materials at the time of planning, purchasing, and certainly before installing. The probability of failures increases with the use of materials with high coefficients of thermal expansion are incorrectly installed (to error is human). Differing metals absorb and reflect sunlight differently and will expand and contract at different rates.
An "OOPS Moment in History:
On the morning of October 28, 1965 - the stainless steel Gateway Arch in St. Louis was slated to be completed with ceremony. The ceremony would showcase the placement of the final keystone at the top of the monument. The piece was hoisted to the top of the structure, only to be five inches too long – it wouldn’t fit! What happened?
The morning sunlight had caused the arch to expand more than expected. The final piece wouldn’t fit until engineers realized their thermal expansion miscalculation. Water had to be sprayed on the south leg of the monument to cool down and contract the structure to make the last keystone fit!